AI-FORM 工業案例
案例 I: DOE 研究模型空間
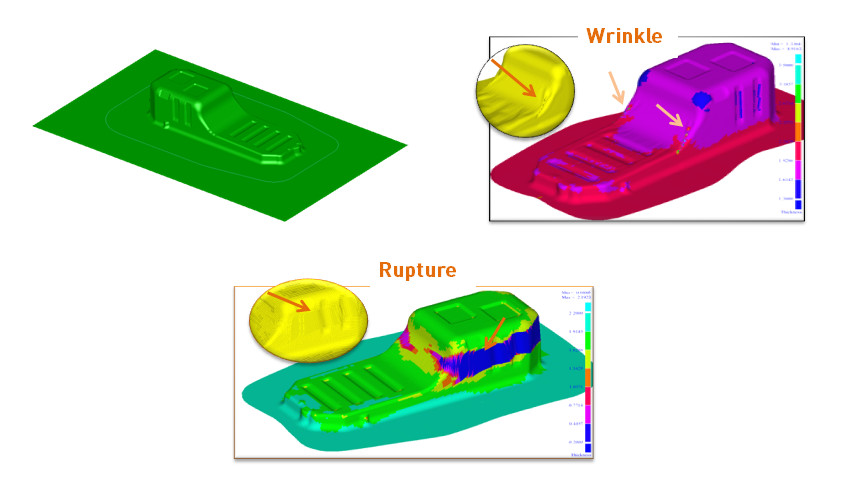
初始模擬的結果,顯示成形後的零件存在嚴重的皺紋和斷裂問題
項目背景
- 汽車油箱形狀複雜,深度不勻,壓邊面積小,零件存在巨大深度落差的鞍部,非常容易起皺和斷裂。需要通過優化調整壓邊力,壓延筋的分佈和初始板材的大小來平衡材料流動,避免缺陷。
- 通常的技術手段是手工調試方案組合,結合衝壓加工仿真程序,對方案進行評估。但是耗時時間長,效率低下,而且很難找到最佳解和工作區間。因此,需要採用集成一體全自動化的優化方法。輔助工程師的方案選型,提高設計效率,節省時間成本。
優化策略
根據初始模擬的結果,確認對如下幾何和變量進行優化,尋找其最佳工作窗口:
- 衝壓板材的尺寸 (下圖中BS的偏移量)
- Drawbead的位置和長度(DB1和DB2的值)
- Drawbead壓延力的大小,從而確定其形狀和尺寸。
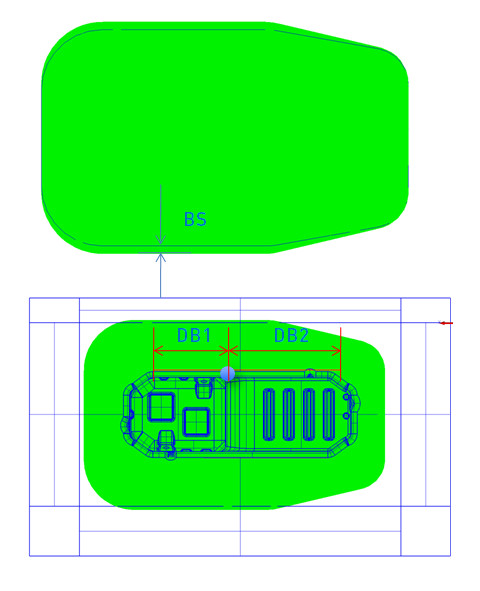
優化策略中的輸入參數示意圖
優化準則
根據初始模擬的結果,將優化目標定義成以下三個目標變量:
- 在鞍部選擇一個區域,根據最大厚度判斷是否存在皺紋;
- 在板材上定義傳感器,獲取最終的板材流入尺寸;
- 在零件頂端定義一個區域,獲取FLD的累積值,判斷是否發生斷裂。
優化步驟
由於工藝範圍很寬,對各輸入變量與輸出結果間的關係尚不清晰且對最佳工作窗口無法預估,也無法預知輸入條件中是否存在滿足最終產品要求的工藝窗口,因此採取兩步進行優化。
第一步: 用DOE尋找可行的工藝窗口
第二步: 採用PSO優化工藝窗口
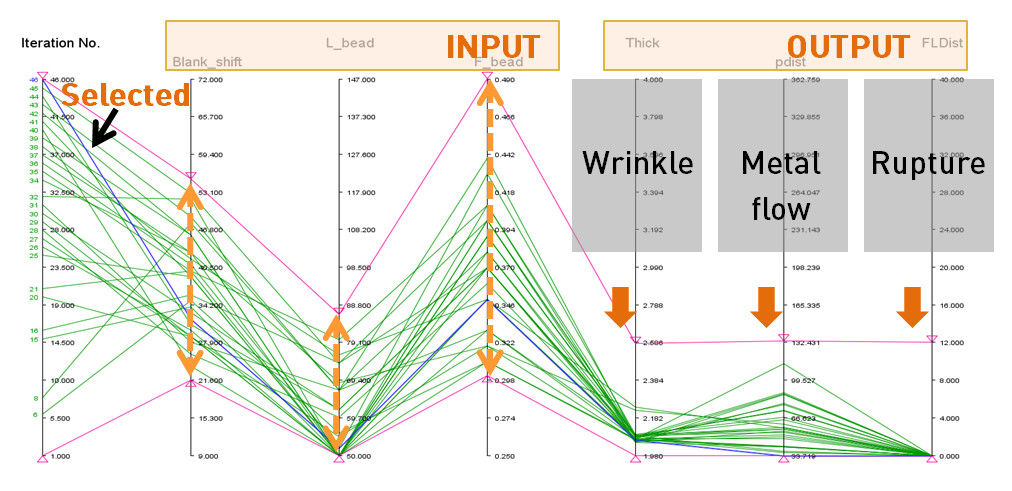
T調整平行座標取值後PSO分析的結果
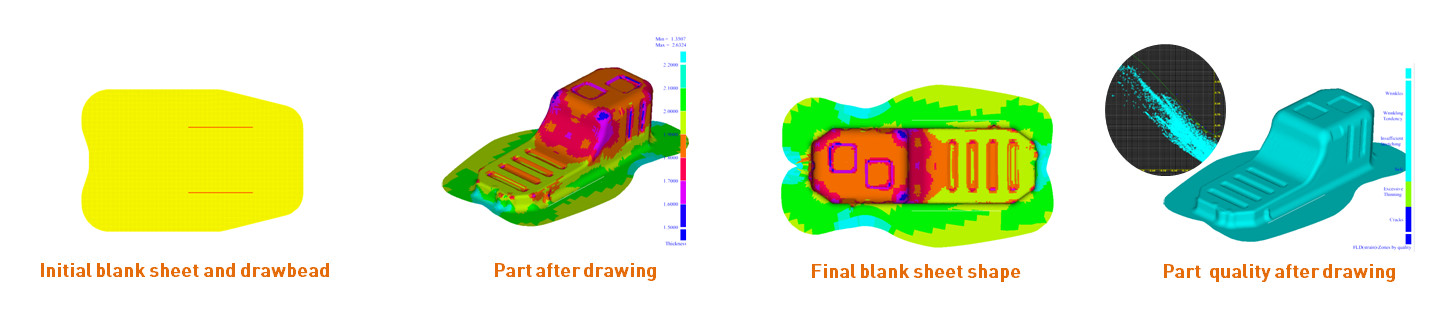
優化工藝區間內的模擬結果(46號)
由於PSO分析是基於DOE分析的結果,所以結果取值範圍已有明顯的改善。通過調節輸出結果軸,可以看到,當板材幾何尺寸偏移量介於21~63, 壓延筋長度介於50~89,壓延阻力系數介於0.29~0.4的範圍內,都能獲得滿意的衝壓結果。
項目總結
- C可現實CAD驅動的自動優化
- 可優化任何尺寸和參數,包括幾何尺寸、材料參數、過程工藝條件等。
- 完全自動化的有限元網格劃分和邊界條件定義,無需人工干預。任何模擬參數均可作為優化準則
- 無限的輸入變量和輸出結果
- 多種優化算法:DOE,GA 和 PSO
- 附帶專業的優化結果過濾與分析工具,例如帕累託圖,平行座標圖等
- 支持並行計算和併發優化。
案例 II: 物理模型空間
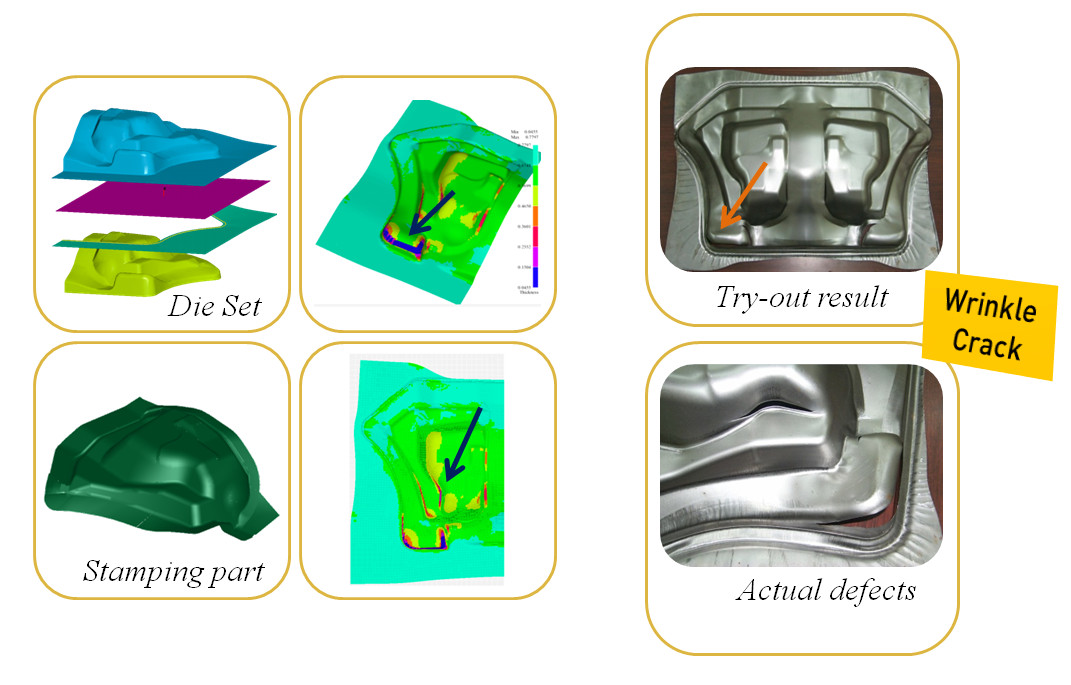
初始設計:模擬結果與實際試模結果比較
項目背景
- 衝壓產品的成形性往往受到其本身幾何特徵的諸多限制,特別是那些遠離入口圓角的特徵,控制的手段非常有限。這樣在實際衝壓中解決起來往往效果不佳。
- 通過修改模面,在壓料階段儘量蓄積更多的材料,在皺紋和斷裂之間進行巧妙的平衡是非常有效的解決方法。但由於問題的非線性,如果只是通過有限數量的手工修改,在缺乏人工智能指導的情況下是非常困難的。
- 本案例針對某汽車零件,說明採用CAD直接驅動優化解決零件斷裂問題的流程和實施要點與解決策略。
優化階段
1, 優化板材形狀和大小
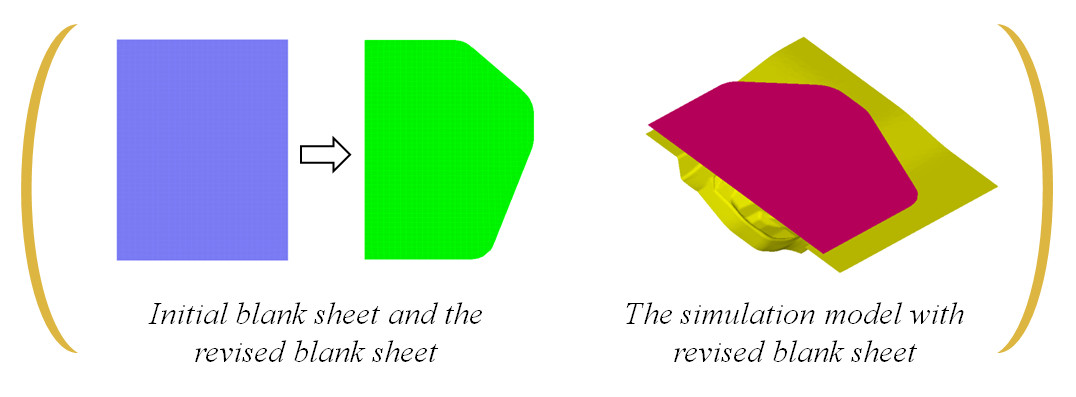
2, DOE瞭解物理問題
- 瞭解衝壓物理問題的實質, 尋找到解決問題的策略,並提取其中影響入料的特徵部分,如本例中的H1和H2,進行參數化研究。
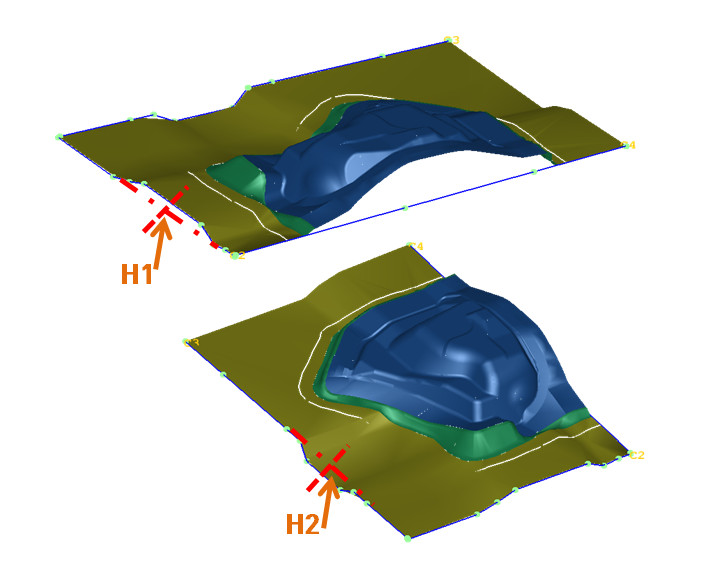
ParaCAD 模型
- 優化工藝參數: 壓延力, 摩擦係數
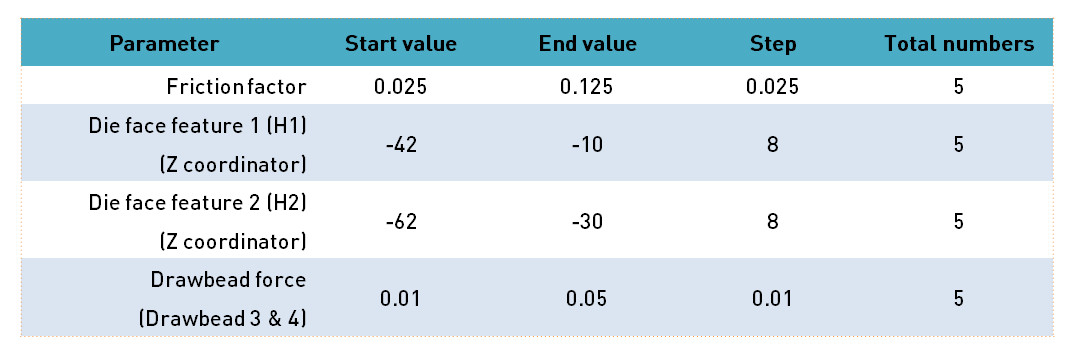
3, 最佳工作窗口
模面參數H2和摩擦係數是主要因數,而模面參數H1和壓延筋阻力是次要因數。 圖中顯示了各變量的影響比例。
從結果分析,以下的工作窗口,均可獲得高質量和衝壓件。
- 摩擦係數: 0.04 to 0.05
- H2: -55.0 to 30.0
- H1: -42 to -10
- 壓延力大小: 0.01 to 0.05
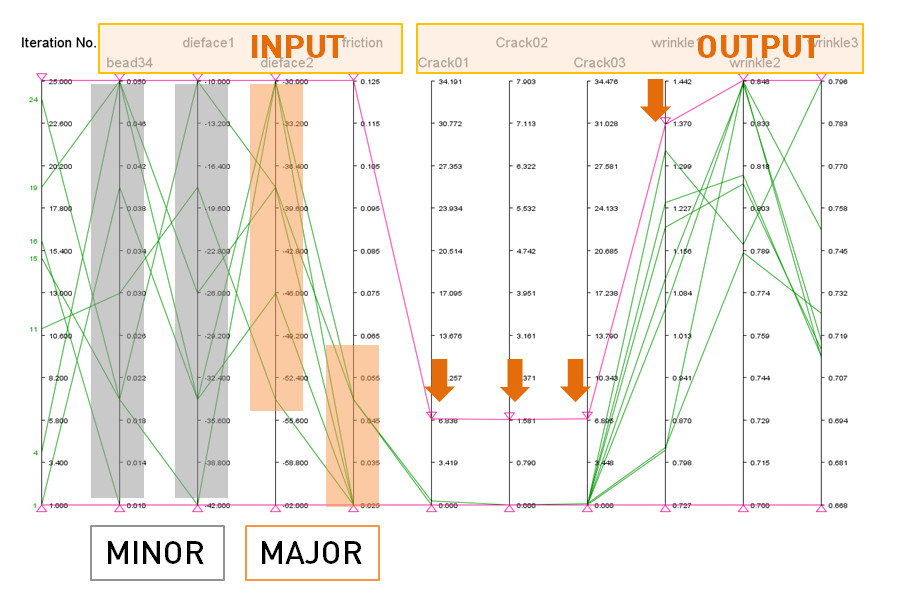
圖中顯示了各變量的影響比例。
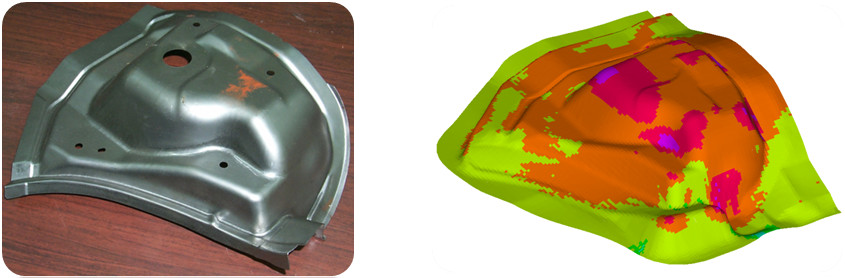
批量生產零件與模擬結果比較
(雲圖為厚度分佈)